Maximize Your Efficiency with Bottle Label Applicators
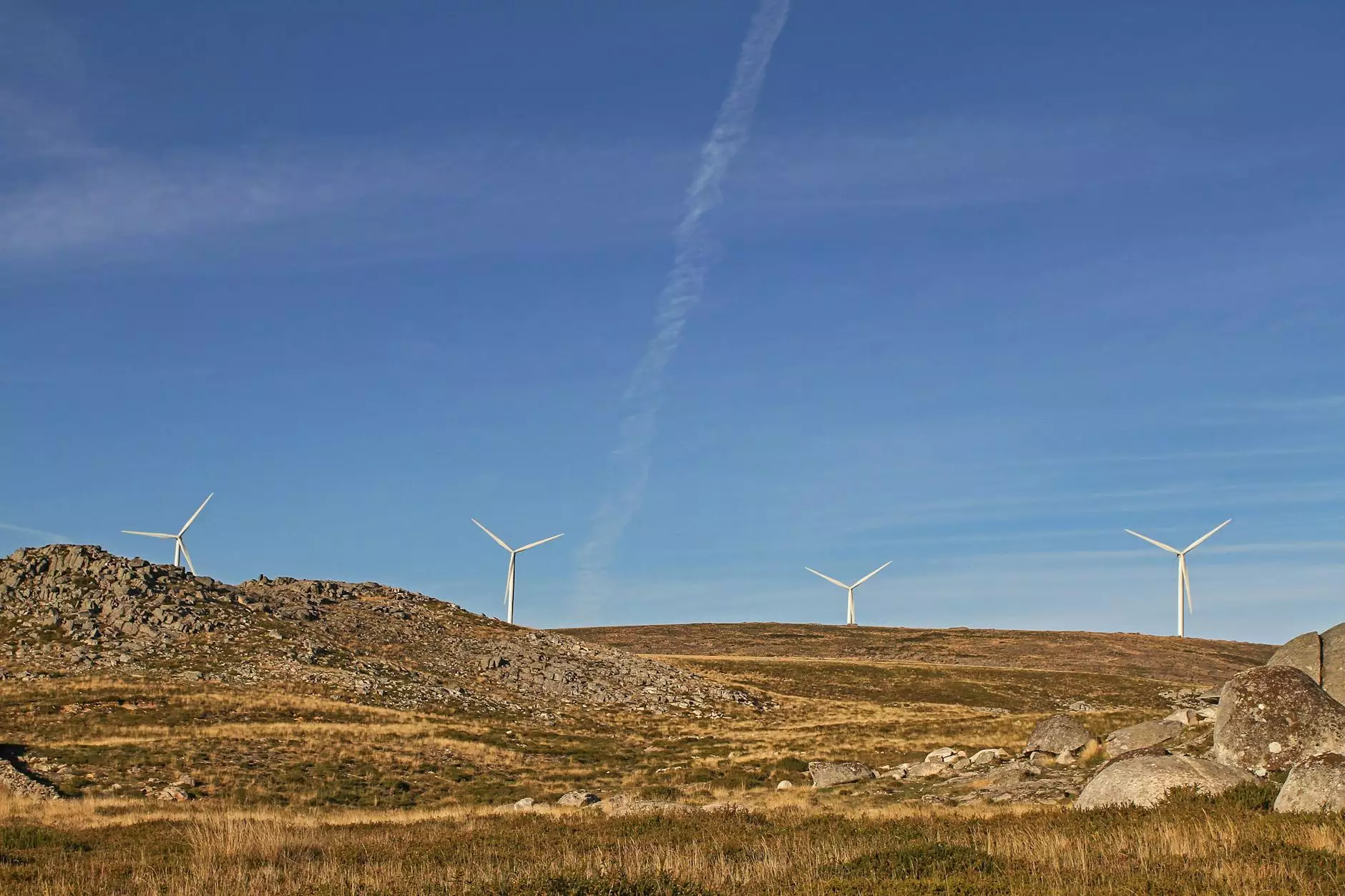
In the bustling world of business, efficiency is key to staying ahead of competitors. In industries ranging from food and beverage to cosmetics, the presentation of products can significantly influence consumer purchasing decisions. One critical aspect of product presentation is labeling, and this is where the bottle label applicator plays a pivotal role.
Understanding Bottle Label Applicators
A bottle label applicator is a machine designed to automate the process of applying labels onto various types of bottles, including glass, plastic, and metal. These machines are essential for manufacturers looking to enhance productivity, ensure consistency, and reduce labor costs. In this article, we will explore the different types of bottle label applicators, their benefits, and how they can transform your bottling process.
Types of Bottle Label Applicators
There are several types of bottle label applicators available on the market, each designed to cater to specific packaging requirements. Understanding these types can help you choose the right applicator for your business.
1. Manual Bottle Label Applicators
For small-scale production, manual bottle label applicators might be the perfect solution. These devices allow users to apply labels by hand, offering a low-cost and straightforward method for labeling products. Such applicators are suitable for startups or businesses with limited labeling needs.
2. Semi-Automatic Bottle Label Applicators
Semi-automatic bottle label applicators combine human effort and automation. They require manual placement of the bottle, but the machine handles the label application process. This type is ideal for businesses experiencing moderate production volumes, providing a balance between efficiency and cost.
3. Fully Automatic Bottle Label Applicators
For large-scale operations, fully automatic bottle label applicators offer the highest level of efficiency. These machines can label hundreds of bottles per minute, dramatically increasing productivity while maintaining precision. Fully automatic applicators are best suited for industries with high demand and large production runs.
Benefits of Using Bottle Label Applicators
The implementation of a bottle label applicator can yield significant advantages for businesses. Let's explore some of the primary benefits:
1. Increased Efficiency
Automating the labeling process allows companies to produce more products in less time. This efficiency translates to faster turnaround times and increased output, enabling businesses to meet consumer demand without unnecessary delays.
2. Enhanced Consistency
Manual labeling can result in inconsistencies due to human error. With a bottle label applicator, each label is applied uniformly, which enhances the professional appearance of the product and improves brand integrity.
3. Cost Savings
While investing in a bottle label applicator requires upfront capital, the long-term savings can be significant. Reduced labor costs and minimized waste due to misapplied labels can lead to lower operational expenses, thus boosting overall profitability.
4. Versatility
Modern bottle label applicators are versatile and can accommodate various bottle shapes, sizes, and types. This flexibility allows businesses to pivot quickly to new products or packaging needs without the need for additional equipment.
Choosing the Right Bottle Label Applicator
When selecting a bottle label applicator, there are several important factors to consider:
- Production Volume: Assess your labeling needs based on your production volume. Smaller operations may benefit from manual or semi-automatic models, while larger operations should consider fully automatic options.
- Bottle Types: Ensure the chosen applicator can handle the specific types and sizes of bottles your business uses. Different applicators have varying capabilities regarding bottle contours and materials.
- Label Materials: Consider the types of labels your products will use, such as paper, vinyl, or shrink sleeves. Ensure the applicator can accommodate these materials effectively.
- Budget: Evaluate your budget for labeling machinery. While fully automatic applicators are highly efficient, they are also more expensive. Balancing budget with functionality is crucial.
- Space Availability: Keep in mind the physical space available in your production area. Some machines require more room than others and may necessitate adjustments to your layout.
Integration with Overall Production Line
The introduction of a bottle label applicator should be part of a larger plan to streamline your production line. Proper integration ensures that your labeling process runs smoothly alongside other processes such as filling, capping, and packing.
Consider the following steps for successful integration:
- Conduct Process Mapping: Identify all steps in your production line to see where the labeling process fits in.
- Choose Equipment that Matches: Select a label applicator that can seamlessly integrate with existing machinery.
- Train Your Staff: Provide adequate training for your workforce to ensure they are skilled in using the new equipment and understand its importance in the overall production process.
- Monitor Performance: After implementation, regularly check the performance of your labeling machinery to identify any potential issues early on.
Future Trends in Bottle Labeling
The world of labeling technology continues to evolve. Future trends may include:
1. Increased Automation
As technology advances, we can expect further integration of automation in bottle labeling. This increase will likely lead to even higher speeds and efficiency in production lines.
2. Eco-Friendly Labeling Solutions
With growing environmental awareness, businesses are looking for eco-friendly labeling solutions. Innovations in biodegradable labels and sustainable applicator technologies are on the rise.
3. Smart Labeling Systems
The future could also see the development of smart labeling systems that use IoT technology to monitor and manage labeling processes remotely. These systems can provide real-time data and analytics for a more efficient operation.
Conclusion
Investing in a bottle label applicator is a crucial step toward enhancing the efficiency and quality of your product presentation. By understanding the various types of applicators, their benefits, and how to integrate them into your production process, you position your business for success in a competitive marketplace.
At omegabrand.com, we understand the importance of quality in printing services and electronics. Explore our offerings to find the perfect labeling solutions that cater to your specific business needs. Take your packaging process to the next level and ensure your products stand out on the shelves.
For any inquiries or to learn more about our services, please visit omegabrand.com today!